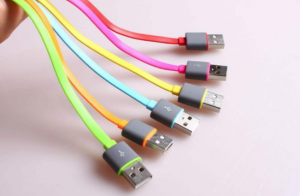
1. Inspection method
Distance: The distance between the human eye and the surface of the measured object is 250mm-350mm
Time: each side inspection time does not exceed 5-10S
Position: The viewing surface is 45 ° from the desktop, turned 15 ° up, down, left and right, flipped back and forth
Light source: D65-CLE standard light source (light source must be directly above the tester)
Temperature: 23 +/- 3 celsius
Humidity: 30% -85%
Light intensity: 1000 ± 200LUX
Vision: The inspector’s vision needs to be above 1.0
Detection tools: caliper, tape measure, ruler
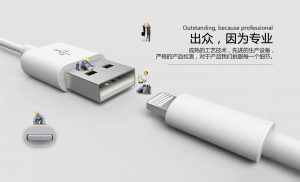
2. Summary of bad defects
Shell cracking: caused by external force or material factors
Deformation: caused by external force interference
Scratches: caused by sharp objects
Shrinkage: molding cooling time is too short
Smudge: environmental factors or grease on the work surface
Oxidation: Blackening of hardware
Thread burns: caused by improper workmanship or operation
The nameplate is affixed: the nameplate is not correctly affixed
Nameplate down: nameplate down
Missing nameplate: Missing nameplate when employees operate
The nameplate is tilted: the nameplate is not in place and not tight
Can’t download: Can’t download songs or videos after connecting to a computer
Not charging: internal device is damaged or other reasons
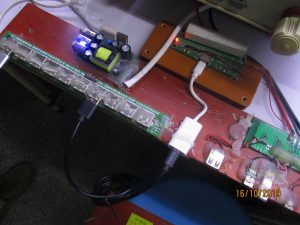
3. Packaging inspection
Check whether the packaging method meets the requirements and whether there is a PASS label or seal affixed by the supplier
Confirm whether the outer packaging specification model, material code, quantity, production date, production batch number are correct
Whether the outer box marking is correct, there must be no incomplete marking and incorrect marking
The outer packing box must not have obvious folds, breakage, dirt, deformation, moisture, etc.
The changed materials must be conspicuously marked, and three batches of markings must be made in succession. If there are special needs, communication and written notification are the main
Packaging needs pad foam protection