1.Appearance
2.Quantity check
3.Smell test
4.Function test
5.Load test
6.Carton dropping test
7.Material check
8.Barcode scanning
9.Water proof test
10.Pull test
11.GSM weight
12.Drop test
China’s gas production to maintain solid growth
BEIJING, March 8 — China’s gas sector exhibited a strong performance in the latter half of 2020 and medium-term growth will remain solid, according to the latest report from Fitch Ratings.
A recovery in industrial activity following coronavirus pandemic lockdowns and an exceptionally cold winter triggered a gas-supply shortage in late 2020, with strong demand leading to higher gas imports, the ratings agency noted.
However, last year’s gas-supply crunch was less severe than that seen in 2017, as national oil companies had moved some long-term contract deliveries to the winter to close the gap, according to the report.
The presence of new liquefied natural gas terminals, storage facilities and pipelines also helped to boost supply.
Fitch said it expects the medium to long-term gas supply to remain firm, driven by solid gas demand momentum.
“National oil companies are steering investment towards gas rather than crude oil in a bid to achieve carbon neutrality while safeguarding national energy,” it noted.
How to Treat the Development of Cloud Economy under the Epidemic
Under the epidemic, the new economy represented by the digital economy quickly fills up its seats to provide protection for everyone’s needs in life. “Cloud Office”, “Cloud Fitness”, “Cloud Concert”, “Cloud Recording”, “Cloud Release”…a business format about “cloud” became standard, which even detonated the term “cloud economy”. Although some people do not understand this concept very well, they have actually participated in it.
There is currently no uniform definition of “cloud economy” in academic circles. Some scholars define “cloud economy” as the economy of cloud computing and cloud services. Joe Weinman, the author of “Cloud Economics-Enterprise Cloud Computing Strategy and Layout”, explained that “cloud economics” is not an esoteric economic theory. The mathematical model is a vivid summary of the technological revolution, the core concept of “flexible cloud computing can effectively enhance the business value of enterprises”. The “cloud economy” we are talking about today mainly defines the business trend of enterprises and society under the massive application of cloud computing.
Since the country put forward the “Internet +” action plan in 2015, “Internet +” has been widely integrated into all walks of life, and the continuous innovation and integration of online scenes and offline scenes has promoted retail, finance, culture and entertainment, medical care, government affairs and other fields The rapid development and the “Internet +” that incorporates artificial intelligence technology is a technology cluster application. From pure software intelligence in the past to hard and soft intelligence today, it has changed people’s daily life and the overall industrial structure. Promoting the consumption upgrade of the market has also played a positive role and has become one of the signs leading the innovation and development of enterprises and society. In this special period of epidemic prevention and control, people rely on online work and life. It is generally believed that this is another rapid development trend in the Internet industry after SARS, which may provide more opportunities for entrepreneurship and employment, or even form new ones. The economic outlet of China-“Cloud Economy”.
Whether it is facial recognition and body temperature measurement equipment, or online check-in and attendance systems, all walks of life are launching various “cloud”-related products. When the market is advancing by leaps and bounds, we should maintain a rational mindset and be cautious and objective about the “cloud economy”. The popularity of the “cloud economy” during this period is mainly affected by the isolation of people at home during special periods, but the most fundamental driving factor is the rapid development of my country’s Internet and logistics industries in recent years. After the epidemic is over, it is a question mark whether the “cloud economy” can continue to be prosperous after being separated from the consumption environment of everyone’s home. In a short period of time, its impact on economic development and entrepreneurship and employment is still limited.
However, it should be noted that during this epidemic, consumers at home took the initiative to apply various “cloud economy” products, which I believe has provided a lot of support for the development of the “cloud economy” industry. The epidemic brings short-term pressure, but also brings opportunities for changes in the industry structure. Take “Cloud Classroom” as an example. The “Suspension of Classes without Suspension” this time is a test of online education. Some pain points such as poor self-control of students in online education have been exposed, and it is believed that the promotion of solving these pain points will become ” The next focus of “wisdom education”. In addition, the formulation and improvement of the “cloud economy” development policy will bring benefits to the better promotion of the development of the “cloud economy” in the future.
After this epidemic, we must not only see the reasons behind the “cloud economy”, but also find new “outlets” from the aspects of economic and social development and lifestyle changes. The government, enterprises and other diversified entities should increase integration and innovation mechanisms to truly endow this new economic form with more vitality and impetus.
China village embodies victory over poverty
Xi Jinping (R), general secretary of the Communist Party of China (CPC) Central Committee and chairman of the CPC Central Military Commission, visits the family of Tang Rongbin, an impoverished villager in the Luotuowan Village of Longquanguan Township, Fuping County, North China’s Hebei province. Xi made a tour to impoverished villages in Fuping County from Dec 29 to 30, 2012.[Photo/Xinhua]
Xi’s visit in 2012 pointed way for nation’s efforts in improving people’s livelihoods
The village where Gu Rongjin has lived for his entire life was on the verge of disappearing 10 to 20 years ago, with few means to support local livelihoods, its young people migrating elsewhere, the farmland unattended and the village school closed.
Luotuowan, a village in Fuping county of Hebei province, located at the foot of high mountains and only about three hours’ drive from Beijing, used to typify China’s rural poverty. Its residents lived on a meager per capita income of 950 yuan ($147) in 2012, and over 79 percent of its residents lived below the official poverty line.
On Dec 30, 2012, the village welcomed an important guest. Xi Jinping was on a tour to assess the real situation of China’s poor areas less than two months after he was elected general secretary of the Communist Party of China Central Committee.
Gu, 73, was then the Party secretary of the village and still has a vivid memory of Xi’s tour. “It was about 9 am, and many of us still hadn’t had breakfast. I remembered him lifting the pot lid to see what was being cooked. He wanted to see the real situation,” Gu recalled in a phone interview.
Sitting down with villagers in their rundown homes, Xi made a powerful appeal about the need to fight poverty.
“As long as we have confidence, even loess can be turned into gold,” Xi said during his visit to the county, in remarks that were published last week by Qiushi, the flagship magazine of the CPC Central Committee.
More than eight years on, as China is set to convene a grand meeting on Thursday in Beijing to summarize its poverty alleviation outcomes and honor outstanding units and individuals who have made key contributions to work on this front, analysts said Xi’s remarks in Fuping pointed the way for China’s poverty reduction effort starting from 2012, mapping out targets and priorities and laying the foundation for the targeted alleviation strategy.
China has secured a victory in its fight to eliminate absolute poverty in rural areas after having lifted nearly 100 million people out of extreme deprivation and ensuring that poverty was eliminated in all 832 national-level poverty-stricken counties by 2020.
“Xi’s remarks on his visit to Fuping emphasized a people-centered philosophy, a key development concept that was fully demonstrated during China’s anti-poverty campaign,” said Huang Jikun, director of the China Center for Agricultural Policy at Peking University.
His remarks also set the tone for the country’s efforts to develop a model for poverty alleviation, including steps to attract participation from private capital and focusing on the capacity building of impoverished groups and areas, he said.
The trip, which marked the beginning of China’s intensified poverty reduction efforts, was followed by a host of inspection tours made by Xi and meetings he chaired focusing on poverty alleviation in recent years.
Xi first set out the targeted poverty reduction strategy during his visit in November 2013 to Shibadong, an impoverished village in Hunan province.
At a national work conference on poverty alleviation in November 2015, Xi expounded on the goals, tasks and major measures in the fight against poverty and called for the use of targeted steps in the process.
He listed the fight against poverty as one of China’s three critical battles in a report to the 19th National Congress of the CPC in October 2017, saying that “poverty alleviation should reach those who truly need it and deliver genuine outcomes”.
China has secured a major victory that is worthy of esteem from the whole world and the country has reshaped the look of its poor areas, improved the conditions of production and life and improved the quality of life of the public during the process, Xi said at a key Party meeting in December.
China is the Only Country Whose Major Economy Achieve Positive Growth in Its Economic Development Report in 2020
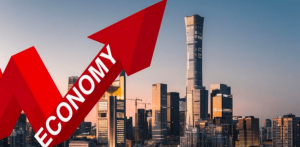
According to the Voice of China’s “News Evening Peak” report, the National Bureau of Statistics announced on the 18th that the gross domestic product (GDP) in 2020 will exceed the 100 trillion yuan mark for the first time, with a growth of 2.3% against the trend. Become the only major economy in the world to achieve positive growth. With the new crown pneumonia epidemic raging around the world, the world economy is in a severe recession, and the external environment is more complicated and severe, how exactly is such a beautiful report card written?
2020 is an extraordinary year in the history of New China. In the face of severe and complex domestic and foreign environments, especially the severe impact of the new crown pneumonia epidemic, my country has submitted an excellent report card. The value was 101,5986 billion yuan, an increase of 2.3% over the previous year. The per capita GDP exceeded US$10,000, the economic structure continued to be optimized, and major engineering projects were basically completed. Ning Jizhe, deputy director of the National Development and Reform Commission and director of the National Bureau of Statistics, said: “The epidemic prevention and control work has achieved major strategic results. The main goals and tasks of economic and social development have been completed, and the completion is better than expected. The 13th Five-Year Plan was successfully completed. Officials, the victory of building a well-off society in an all-round way is in sight.”
A decisive victory was achieved in the decisive battle against poverty. Under the current standards, all rural poor people have been lifted out of poverty, 832 poor counties have all been removed, absolute poverty has been eliminated historically, and 55.75 million rural poor people have been lifted out of poverty. In 2020, the seven provinces (regions) of Guangxi, Sichuan, Guizhou, Yunnan, Gansu, Ningxia, and Xinjiang, where there are more poor people, the nominal growth rate of per capita disposable income of rural residents is 0.2-1.7 percentage points higher than the national growth rate of rural residents. The macro-control has achieved remarkable results.
Ning Jizhe said: “The quarterly economic growth indicators have returned to normal levels. In the fourth quarter, GDP grew by 6.5% year-on-year, 0.7 percentage points higher than the same period of the previous year. In 2020, 11.86 million new jobs were created in cities and towns across the country, exceeding the full year. Goals and tasks. In 2020, the consumer price index CPI will increase by 2.5% over the previous year, which is lower than the expected target of about 3.5%. In 2020, the national per capita disposable income will increase by 2.1%, which is basically in line with economic growth.”
The implementation of “six stability” and “six guarantees” has achieved remarkable results, and reform and opening up have created miracles of development. The benefits of multiple ownership enterprises have been improved. Ning Jizhe introduced: “In 2020, the added value of high-tech manufacturing will increase by 7.1% over the previous year, 4.3 percentage points faster than the added value of all regulated industries. The growth of foreign trade and foreign investment is better than expected, and global trade and cross-border investment will shrink sharply. Under the circumstances, my country’s total imports and exports of goods in 2020 hit a record high, an increase of 1.9% over the previous year. From January to November, the actual use of foreign capital increased by 6.3% year-on-year.”
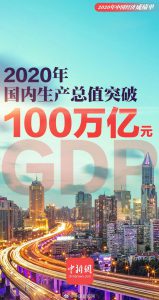
In 2020, the total economic volume will exceed the one-hundred-billion-yuan mark. Ning Jizhe emphasized that this means that my country’s economic strength, scientific and technological strength, and comprehensive national strength have jumped to a new stage. It is of great landmark significance for building a well-off society in all respects and starting a new journey of building a socialist modern country in an all-round way. He pointed out: “Within 20 years, the total economic scale will be expanded to 10 times, and the achievements have attracted worldwide attention. In 2020, my country’s GDP will reach about 14.7 trillion US dollars, ranking second in the world, and accounting for 17% of the world economy. Around. In 2020, the per capita GDP will exceed 10,000 U.S. dollars for two consecutive years, stabilizing the ranks of upper-middle-income countries, and the development gap with high-income countries will continue to narrow.”
“You can go up to nine days to capture the moon, and you can go down to the five oceans to catch turtles” has become a reality. Technological innovation is becoming more and more active, injecting new vitality into high-quality economic development. my country’s industrial and agricultural production capacity has increased significantly. The total grain output hit a record high and continues to rank first in the world.
“The output of more than 220 kinds of industrial products ranks first in the world, and the added value of manufacturing is expected to rank first in the world for 11 consecutive years. The infrastructure continues to improve, and the total operating mileage of high-speed railways has reached 38,000 kilometers and the mileage of expressways has exceeded 155,000 kilometers. The number of 5G terminal connections has exceeded 200 million, ranking first in the world.” Ning Jizhe said.
More importantly, this has laid a solid foundation for my country to build a new development pattern. Ning Jizhe said that the key to accelerating the formation of a new development pattern in which domestic and international cycles are the mainstay and the mutual promotion of domestic and international cycles lies in tapping the potential of domestic demand, especially consumer demand. He introduced: “my country’s population ranks first in the world, and the middle-income group is also the largest in the world. In 2020, the total retail sales of consumer goods will be close to 40 trillion yuan, the final consumption expenditure will exceed 55 trillion yuan, and the total capital formation will also be close to 45 trillion yuan. This will help my country’s superior market size to be further brought into play.”
In the past year, the total retail sales of consumer goods continued to show negative growth throughout the year, down 3.9% from the previous year. However, the third and fourth quarters have turned positive, especially in the fourth quarter that the total retail sales of consumer goods increased by 4.6%. This rate has begun to approach the normal level of previous years. Ning Jizhe said that my country’s consumption is still the ballast stone for the stable operation of the economy! “From 2011 to 2019, my country’s consumption rate averaged 53.4%. In 2020, despite the impact of the new crown pneumonia epidemic, the final consumption expenditure accounted for the proportion of GDP. It still reaches 54.3%, which is 11.2 percentage points higher than the total capital formation, and is the highest level in recent years. Consumption is still the ballast stone for the stable operation of the economy.”
Ning Jizhe said that due to the epidemic, the growth rate of total social consumer retail sales fluctuated slightly in December, but from the overall trend, my country’s consumption was able to play a fundamental factor in economic development while increasing production and supply. Looking forward to 2021, there are many favorable factors that support the stable recovery of the economy. my country’s economy has a foundation and conditions to continue its steady recovery. Although the current pressure on the prevention and control of the epidemic to “import from external defenses and rebound from internal defenses” is still great, the fundamentals of my country’s long-term economic improvement have not changed.
“The obvious institutional advantage is the fundamental guarantee for economic stability and long-term social stability. Although the epidemic has spread in some places recently, the overall impact on the economy is controllable. We have the conditions and ability to control the spread of the epidemic and operate the economy. Stay within a reasonable range to achieve sustained and healthy development of the Chinese economy.” Ning Jizhe said.
Keyboard Quality Control Inspection Service
1.Appearance
2.Quantity check
3.Barcode Scan
4.Material check
5.Basic function check (Assembly)
6.Rubbing test
7.Odor test
8.Bluetooth device selection and connection
9.Bluetooth 10m distance test
10.FN multimedia function
11.Sleeping set function
12.Battery charge test
13.USB/BT mode switch
14.Standby current
15.Working current
16.Battery discharge test
17.Inner structure and electronic check
Large Mower Quality Control Inspection Service
Some common factors for large mower quality control:
Appearance
Quantity check
Measurement(major size)
Basic function test(Functions on product specification work)
3M tape test for Logo
Barcode scanning
Electric water heater inspection
1. Visual inspection standards and inspection methods:
Surface grade
Class A surface: an external surface that can be viewed directly, such as the front and front sides of an electric water heater, hereinafter referred to as the A surface.
Class B surface: Inconspicuous external surfaces, such as the rear and rear surfaces of electric water heaters, hereinafter referred to as the B surface.
Class C surface; internal and external surfaces that are not easily visible, such as the floor surface of electric hot water, hereinafter referred to as the C surface.
Inspection environment
Luminosity: Normal light or 200-300LX (equivalent to a distance of 750mm for a 40W fluorescent lamp) The inspection surface of the product should be approximately 45 ° from the visual direction of the inspector.
The distance between the inspector’s visual direction and the surface of the product to be inspected is as follows:
A surface: 400MM B surface: 500MM C surface: 800MM
Degree of defect
Basic method for judging the degree of surface defects: under a standard inspection light source, the distance from the observation object is 400mm, and it should be at an angle of 45 degrees with the observation surface. Defects that are not visible at a glance are slight defects, visible at a glance, but not very obvious, are general defects. Visible and obvious defects are serious defects, and defects that are visible at a glance and seriously affect the appearance are fatal defects.
Defect sampling
Appearance is based on 1dm2. The 11.3cm circle selects the most defects.
Inspection methods and inspection standards
The A side should be smooth and flat with no obvious defects. No serious defects are allowed. No hand-painting is allowed to repair defects. Minor defects are allowed. No rough feeling or deformation can be felt by hand. The insignificant general defects have a diameter greater than 1mm is not allowed, less than 1mm is not allowed to exceed 10 points, and the concentration is not more than 3 / cm2. For non-orthographic planes, the standard can be appropriately relaxed. In the detection area, the diameter is less than 1mm. It is not allowed to exceed 15 points, and the concentration is not more than 3 / cm2.
The B surface should be smooth and smooth without obvious defects. No serious defects are allowed. Minor defects are allowed, and there is no rough feeling or severe deformation when touched by hand. Non-obvious general defects are not allowed in the detection area with a diameter greater than 1.2mm and less than 1.2. mm is not allowed to exceed 20 points, and the concentration is not to exceed 3 / cm2. For non-orthographic planes, the standard can be appropriately relaxed. In the detection area, the diameter is less than 1.2mm. It is not allowed to exceed 30 points, and the concentration is not more than 3 / cm2.
The C-plane allows the presence of general defects and serious defects that do not affect the appearance quality. The splicing gap is less than 1mm, which is acceptable. If it is more than 1mm but less than 1.5mm, it can be conceded according to the actual situation, and more than 1.5mm is unacceptable.
Signs, stickers, print inspections
Check the position of the signs, logos, stickers, and silk screens in accordance with the technical data to check that they are accurate, flat, and free from obvious skew. Failed.
Inlet and outlet pipe inspection
Check the water inlet and outlet pipes. The mouth of the pipe should be smooth and smooth, and the wire teeth should not be damaged and no obvious skew. Meet the requirements as qualified, otherwise as unqualified.
The exposed length of the inlet and outlet pipes should meet the design requirements. The length of the inlet and outlet water pipes shall meet the design requirements.
2. Structural parameter inspection standards and inspection methods
Dimension inspection
The overall dimensions of the product and the dimensions of the packaging box need to meet the dimensions and tolerance requirements of the design drawings, and those without tolerances are implemented as free tolerances.
Inspection with external dimensions
The size of the external fit must meet the size and tolerance requirements of the design drawing, and the free tolerance is implemented if no tolerance is marked. The outer cymbal fittings should be free from obvious skew.
Content volume inspection
Fill the container with water, put it on the weighing scale using a measuring bucket, and gradually pour the water from the product into the measuring bucket, and finally get the total water storage. The minimum content should meet the relevant capacity standards of the country or country of use, or the minimum allowable capacity requirements confirmed by the customer.
3. Inspection standards and inspection methods for hidden structural parameters
Quality inspection of slush layer
Use the light method to check the quality of the inner slush layer. The surface of the slush layer should be milky white, and there should be no burnt black, scars, cracks, whitening, puncture points, and debris in the slush layer. qualified.
Use light reflection perspective inspection or thickness gauge to check the thickness of the slush layer. The light reflection perspective inspection of the surface of the slush layer should show a uniform milky white, and there should be no gray-black shadows of the perspective substrate color (indicating that the slush layer is too thin). The minimum thickness measured by the thickness gauge should be more than 1.5mm, otherwise it is unqualified.
Foam layer thickness inspection
Using the thickness probe, take a point from the appearance and insert it into the shell to contact the liner, and measure the thickness of the foamed layer in each part. The thickness of the foamed layer should meet the design requirements. Those who meet the design requirements are qualified. If the area does not meet the design requirements but the area does not exceed 10%, and the error does not exceed 2mm, it may be conceded in consideration of the actual situation, otherwise it is unqualified.
Foam layer density test
Take a piece of 50X50X40 foam from both ends and the middle of the product, cut off the outer skin layer, and measure the density of the sample to calculate the average density. The average density should meet the designed density requirement, and the lowest density sample density must meet the minimum density requirement. Otherwise it is disqualified. The normal density requirement is 32 ~ 38KG / M3.
Tightness test
The products are connected into a system by using standard external connection accessories, and the normal work is performed under the use conditions. There must be no leakage at any connection parts, otherwise it is unqualified.
The inner tank is tested in accordance with the tightness test method, and there should be no leakage or leakage, otherwise it is unqualified.
4. Electrical safety performance inspection standards and inspection methods
4.1 Inspection of circuits and electrical components
Circuit and electrical device inspection
The electrical components are installed correctly, especially the switches, thermostats, and wiring cannot be reversed, incorrectly connected, or incorrectly connected. The installation of electrical components must be safe and reliable. Under the condition of limited pulling, pushing and pulling, the live parts of electrical components should not touch the metal parts such as the inner liner, screws, or heating parts. Cause the connection cable to be too tight.
There must be no foam, adhesive tape, screws, or metal parts spilling from the end cap.
The wiring and cable ties must be neat and reasonable. The connecting wires must not touch the sharp angles. The connecting pipes of the thermostat and temperature limiter probes must not be flattened.
Safety distance inspection of electrical components
Check that the distance between all exposed wires and terminals and metal parts should exceed the minimum distance required by safety regulations. All connecting wires and accessories should be firmly fixed. Under shaking and slight force, the distance from metal parts should still exceed the minimum safety distance. .
Ground wire safety connection check
The ground wire should be connected with standard yellow-green wires, and the connection fittings should be made of copper. The connection should be firm and reliable and should not be loose. Ground line signs, L, N and other signs must be correct, clear and durable;
Circuit connector safety test
Shake and pull the terminals and wires by hand, and the terminals, wires and screws should not loosen or fall off.
Functional check
Check whether the switch, indicator light and temperature control can work and indicate normally.
Maneuverability check
The knob must be flexible, smooth, and pointed correctly; the switches and keys are correct and reliable;
Accessories stability check
Use one hand to hold the case where the power cord enters, and hold the power cord with the other hand, and push it in and out twice. The power cord must not go in or out more than 2mm, and the power cord cannot be hung or broken. When it is pulled off, the screws holding the wire clamp must not be loose;
4.2 Ground resistance test
Ground resistance test
Insert the plug of the electric water heater into the socket of the ground resistance tester, and then clamp the ground wire clip to the water nozzle of the electric water heater or the hanger without spraying, start the ground resistance tester, and read the resistance value is not greater than 0.1 ohm (100 millimeters) (Europe) is qualified, otherwise it is disqualified.
The standard for grounding resistance is 25A 5S not more than 0.1 ohm (100 milliohms).
4.3 Withstand voltage test
Pressure test
Plug the electric water heater with a qualified grounding resistance into the socket of the withstand voltage tester, press the reset button of the leakage protection switch, adjust the switch and the thermostat to the on state, and start the withstand voltage tester without breakdown or flicker. To be qualified, breakdown, flashing, arc flash, and smoke were unqualified. The standard of withstand voltage is 1800VAC 5S without breakdown and flicker.
Note: During the pressure test, never touch the metal part of the water heater!
4.4 Leakage current test
Leakage current test
Press the reset button of the leakage protection switch of the electric water heater that has passed the withstand voltage test, adjust the switch and the thermostat to the on state, insert the plug of the electric water heater into the socket of the leakage current tester, and dial the L, N switch, read out the leakage current value in the L and N states, the leakage current per kilowatt is less than 0.75mA is qualified, otherwise it is unqualified.
The leakage current standard is 233VAC 5S leakage value <0.75mA / KW. Our company requires that the leakage current standard of each electric water heater is 233VAC 5S leakage value <0.75mA.
When testing the leakage current, check whether the switches and indicators can be lit and correct. Note: When testing the leakage current, the metal part of the water heater is live!
4.5 Power test
Power test
Insert the water heater plug that passed the leakage current test into the socket of the electrical parameter tester, turn on each switch one by one, and read out the corresponding power. The measured power is 0.9 ~ 1.05 times the rated power is qualified, otherwise it is unqualified.
4.6 Functional test
Heating test
Use heating according to the normal use state, check whether the temperature controller is normal, whether the switch is normal, whether the indicator light is normal, whether the inner tank water is normal heating, short the temperature controller, and check whether the temperature limiter can work normally. Everything is normal, otherwise it is unqualified.
5. Other inspection items
Stress safety test
Use an external air source to pressurize the tank filled with water to the take-off pressure of the safety valve, and check whether the safety valve takes off normally. When the pressure of the inner tank reaches the rated pressure of the safety valve, the normal pressure of the safety valve is qualified and abnormal. Failed.
Inject the liner into 90% water, then immerse the liner into the pool, increase the liner pressure to twice the use pressure, stabilize the pressure for 10 minutes, and observe whether the liner has changed. After the pressure was released from the liner, the shape was qualified if it did not change, and the shape appeared deformed and distorted, and even failed.
Liner fatigue test
Connect the bladder to the fatigue tester, and perform the pressure and pressure fatigue test. The frequency setting and frequency are performed according to the relevant product technical requirements. After the fatigue test is completed, the bladder is qualified if there is no obvious deformation and leakage. After the fatigue test is completed, In the case, obvious deformation and leakage of the inner liner were unacceptable.
Thermal insulation test
Warm the water in the product to the set temperature, turn off the heating power, place it naturally for 24 hours in a standard environment, measure the temperature to reduce the temperature difference, calculate the insulation performance parameters, and meet the relevant requirements of the country and the country of use as qualified, otherwise it is unqualified .
Thermal yield detection
The product is warmed up to the set maximum temperature. After reaching the temperature, it stays stable for 10 minutes. Measure the temperature of the water and then close the water inlet valve. Pour the hot water in the machine into the insulation bucket and mix it uniformly. Measure the temperature after mixing. And the temperature after mixing, calculate the heating rate of the liner water.
The product is heated from the set temperature to the set maximum temperature. After reaching the temperature, it stays stable for 10 minutes. Turn off the power, use a 45-degree thermostatic valve to drain water into the measuring barrel, and keep it until the outlet temperature is lower than 42 degrees. The amount of water and product content were used to calculate the thermal yield.
Suspension strength test
Fill the product with water and hang it on the suspension test wall, and then use the weighting block to double the weight of the product and suspend it for 4 hours. Check whether there is deformation in the hanger and the shell. Damage is qualified, otherwise it is unqualified.
Freezer test
Put the product in a -30 degree freezer, store it for 12 hours, take it out to restore the temperature at ambient temperature, and check whether the shell is deformed or broken. If there is no obvious deformation and crack, it is qualified, otherwise it is unqualified. Then test whether the product can still work normally, it can work normally and the electrical performance test is qualified, otherwise it is unqualified.
Water Flosser Quality Control Inspection Service
Some common factors for Water flosser quality control:
Appearance
Quantity check
Measurement(weight & size)
Assembly test
Waterproof test
Leaks water test
Water jet impact test
Noise test
Hi-Pot test
Charging test
Open/close function check
Power test
2 minutes automatic shutdown test
Water tank volume test
Basic function check
Barcode scan
3M tape test for Logo
Ultrasonic pest repeller Quality Control Inspection Service
1.Appearance
2.Quantity check
3.Smell test
4.Function test
5.Internal check
6.Dry/wet rub test
7.Material check
8.Barcode scanning