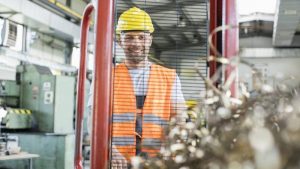
The fundamental reason for the sustained and rapid growth of China’s economy over the past 30 years of reform and opening up lies in the establishment of a manufacturing strategy that suits the national conditions, that is, to take advantage of China’s labor force and market advantages, participate in the international division of labor, integrate into the value chain, and become World Factory.
From the historical experience, the rise and decline of a country’s economic strength has a lot to do with the degree of industrialization. The transfer of economic power in a large country is based on the change in the status of the manufacturing industry.
Therefore, the improvement of China’s overall national strength and economic competitiveness depends on the industrialization process and the rise of the manufacturing industry, thereby establishing the world’s most complete industrial category, the largest scale, and the strongest supporting capabilities of the manufacturing system.
However, after more than three decades of development, China’s manufacturing industry has faced multiple challenges in recent years.
On the one hand, marked by Germany’s proposal of Industry 4.0, the world has entered a period of rapid development of a new round of industrial revolution and industrial competition. Advanced manufacturing countries such as Europe, the United States, and Japan have put forward their own strategies for the development of emerging industries in order to grab the commanding heights of high-end manufacturing in the digital age.
On the other hand, the labor cost advantage that China’s manufacturing industry relies on is gradually being lost as the demographic structure changes. The wages of ordinary workers continue to rise rapidly, and the phenomenon of difficulty in recruiting and expensive labor in the southeast coastal areas has led to the start of new industrial transfers in China’s labor-intensive manufacturing industries, which have flowed to Southeast Asian countries.
As a wrestling field for large countries to participate in global technology and industry competition, the use of advanced manufacturing technologies to promote labor saving, efficiency and cost reduction has become the due meaning of manufacturing transformation and upgrading and sustainable development. China cannot miss this economic structure. Opportunity for adjustment.
At the same time, emerging middle-class consumers are increasingly demanding in terms of quality, functionality, and design of manufactured products. Not only must it meet basic use values, but it must also have certain aesthetic, trend, and even artistic values. This is a personalized consumer experience and psychological satisfaction. Changes on the demand side force the supply side to develop in the direction of high-quality, personalized, customized, and rapid iterative products.
Therefore, in 2015, the State Council issued the “Made in China 2025” strategy to promote China’s transition from a large manufacturing country to a strong manufacturing country. The report of the 19th National Congress of the CPC emphasized that on the one hand, it is necessary to accelerate the development of advanced manufacturing and promote the deep integration of the Internet, big data, artificial intelligence and the real economy; on the other hand, it is necessary to support the optimization and upgrading of traditional industries and promote China’s industry to move into the global value chain. High-end, cultivate a number of world-class advanced manufacturing clusters.
In the implementation of this series of new development concepts and strategies, the transformation path of China’s manufacturing industry has gradually become clear, that is, to promote the transformation of production methods by promoting “machine replacement” and the construction of industrial automation and information technology with the Industrial Internet as the main content. Achieve smart manufacturing.
1 Machine substitution
As early as 1970-1980, the United States, Japan and other countries proposed the concept of industrial automation, mainly to solve the problem of adverse effects on people and the production environment in industrial manufacturing, such as waste of resources, production instability and variability, etc. .
Due to the low labor cost in China in the past, the economic benefits of large-scale automation are not obvious, so there is no need to vigorously promote it. However, under the impact of “labor shortage”, “machine replacement” becomes inevitable, is the core of industrial transformation, and is the basis for the development of the Industrial Internet.
The Industrial Internet refers to the industrial and application ecology formed by the full-scale and deep integration of the Internet and the new generation of information technology and industrial systems. It is a key comprehensive information infrastructure for the intelligent development of industry.
Its essence is based on the network interconnection between machines, raw materials, control systems, information systems, products and people. Through the comprehensive depth perception of industrial data, real-time transmission and exchange, rapid calculation processing and advanced modeling and analysis, it can realize the transformation from a single machine. Intelligent decision-making and dynamic optimization to production lines, workshops, and even entire plants.
It can be seen that the development of the Industrial Internet is based on the automation and informatization of the manufacturing process, and it is moving towards data and intelligence.
Taking Guangdong Province as an example, since 2014, governments at all levels have successively introduced policies to promote technological transformation of enterprises and implement “machine substitution” and “equipment substitution”. For example, the Dongguan Municipal Government successively launched the “About Accelerating the Promotion of Industry” in August 2014. “Implementation Opinions on the Development of Robot Intelligent Equipment Industry”, “Dongguan City’s Action Plan for Promoting Enterprise” Machine Substitution “(2014-2016), and” Mechanical Substitution “Measures for Fund Management.
The Foshan Municipal Government formulated the Implementation Plan of Foshan Supporting Enterprises to Promote the Application of Robots and Intelligent Equipment (2015-2017) in May 2015; the Guangdong Provincial Government formulated the Guangdong Intelligent Manufacturing Development Plan (2015-2025) in July 2015 ) “.
From the perspective of the promotion effect of the policy, in 2017, Guangdong Province had 156 key robot manufacturing enterprises, and the province’s industrial robot output was 20,662 units, a year-on-year increase of 50.2%, accounting for 16% of the country’s output, and the holding amount was about 80,000 units.
Specifically, in Dongguan, from September 2014 to January 2017, enterprises applied for a total of 2698 “machine substitution” special fund projects, with a total financial investment of approximately 38.6 billion yuan, 76315 new equipment and instruments, and the number of projects and investment. Both rank first in Guangdong Province.
In Foshan, from 2015 to 2017, the municipal government financed a total of 160 million yuan, supporting 368 projects, and driving more than 400 enterprises above designated size to carry out “machine substitution” and more than 7,000 robots.
On this basis, starting in 2017, Guangdong took the lead in the nationwide deployment and advance development of the Industrial Internet as a new engine point for the transformation and upgrading of the real economy and manufacturing industry, and to achieve high-quality development by promoting the digital transformation of enterprises.
In March 2018, the “Implementation Plan for Deepening the” Internet + Advanced Manufacturing “Development of Industrial Internet in Guangdong Province” and “Several Supporting Policies for Guangdong Province to Support Enterprises on the” Cloud on the Platform “to Accelerate the Development of Industrial Internet (2018-2020)” were issued, It is expected that through policy guidance, Guangdong will promote 10,000 industrial enterprises to implement digital and network-based intelligent upgrades on the platform, driving 200,000 enterprises to “on the cloud and on the platform” and reducing the cost of information construction.
The purpose of “Upper Cloud Platform” is to realize the interconnection and interoperability of production and manufacturing links such as R & D design, production control, equipment control, process improvement, energy consumption optimization, and supply chain coordination, as well as data connection on the equipment side and management side.
These data will automatically determine the decision of each link of the production system, and realize the integration of upstream and downstream production. The ultimate goal is to analyze the data to forecast demand, forecast manufacturing, and use the data to integrate the industrial chain and value chain to create new knowledge and value.
2 Directions
As manufacturing processes and business activities become more complex, relying on human experience and analysis, it is no longer possible to meet such complex management and collaborative optimization needs, so big data is bound to rise in the industrial field.
Big data is an important feature of the Industrial Internet, because in the process of “machine replacement”, the controller of the automation equipment will generate a large amount of data. With the development of sensor technology and communication technology, the cost of collecting real-time data is no longer No matter how expensive it is.
The rise of embedded systems, low-energy-consumption semiconductors, processors, and cloud computing has greatly increased the computing power of the device and has the ability to process large data in real time.
The Industrial Internet realizes the status of production sites, collaborative enterprise information, and market user needs through the collection and exchange of massive data, the integration and processing of heterogeneous data, edge computing of machine data, solidified iteration of empirical models, and cloud-based big data calculation and analysis. Accurate calculation and complex analysis, thus forming management decisions for enterprise operations and control instructions for machine operation, driving the intelligence and optimization of machinery and equipment, operation management, and business activities.
Realizing the interconnection of industrial robots and other automation equipment, and collecting and analyzing production data are generally recognized directions for the development of the Industrial Internet in China. However, how to use industrial big data and the mining of business value need to be further tested by the market.
Therefore, at this stage, the construction of the industrial Internet infrastructure should be strengthened, especially to enable small and medium-sized manufacturing enterprises to gradually increase their level of automation and informationization, improve production efficiency, and find new business models for data utilization.
Although the Industrial Internet is still a new thing, the author found in the survey that some enterprises in Guangdong have begun to actively use the Industrial Internet for digital transformation. In addition to the application of industrial robots and other automation equipment, more and more enterprises have begun to introduce enterprises. Resource Planning (ERP) and Manufacturing Execution System (MES).
ERP is an enterprise information management system that integrates material resources, capital resources and information resources for the manufacturing industry. Its main functions include supply chain management, sales and marketing, distribution, customer service, financial management, manufacturing management, and inventory. Management, plant and equipment maintenance, human resources, reporting, manufacturing execution systems, workflow services, and enterprise information systems.
MES is to optimize the management of the entire production process by ordering the product to the completion of the product through information transmission. MES needs to collect a large amount of real-time data in the production process and make timely processing of real-time events, while maintaining two-way communication capabilities with the planning and control layers, receiving corresponding data from the upper and lower layers, and feeding back processing results and production instructions.
This production mode considers the planning and scheduling of the manufacturing system, tracking, monitoring and control, material flow, quality management, equipment control, and computer integrated manufacturing interface as a whole, so as to ultimately implement the automation of the manufacturing process.
MES has great potential and development space in solving the pain points of Chinese manufacturing enterprises. The current pain points facing manufacturing companies mainly include the lack of timely control of production progress, passive maintenance of equipment maintenance, inadequate staff skills, slow action during abnormal production, slow response to order tailing, production schedules failing to reach the production line, and the delivery cycle is too long. Long, resulting in orders not being delivered on time.
Due to uneven staff skills, long product switchover times, intelligent departments are too slow to respond to field problems, and abnormal data cannot be reported in time, resulting in low production efficiency.
Due to the formalities of the first article inspection, uncontrolled key positions, rework of defective products, and failure to strictly implement the rework process, customer complaints could not be traced back to specific positions and no materials, data analysis was not systematic, improvement effects could not be verified, and quality problems were frequent hair.
Due to the random loss of materials, it is impossible to adjust the staffing in time according to the production process, the number of work in process is large, and it cannot be quickly resolved. The manual statistical production report has a large workload and poor timeliness, resulting in excessive manufacturing costs.
For example, in Shunde, Guangdong, the home appliance manufacturing industry has the advantage of a complete industrial chain, but the consumer market places higher requirements on product quality. How to solve the problems of low efficiency of the factory, too many workers on the job site, and too long logistics distance in the factory have become urgent matters.
Practice shows that the application of the MES system will promote internal efficiency, the management of defective products, and the management of various aspects have reached a level. For small and medium-sized enterprises, embracing the Industrial Internet is not unattainable. At present, some platform vendors have launched more “small, refined, light” system rental services that can be accurately resolved for enterprises with only tens of thousands of yuan each year. Pain points of the entire production process.
The author had an in-depth exchange with the product manager of a well-known MES company in Guangdong. This lean intelligent factory systematic solution provider is mainly for small and medium-sized manufacturing enterprises on-site management. It provides SAAS based on industrial Internet, microservices, cloud computing, Internet of Things, big data technology architecture with low cost, fast deployment and easy operation and maintenance. Application, to realize the data and transparency of the workshop, improve production efficiency, reduce production costs, reduce material waste, and strengthen quality control.
“Using the JAWA microservices Internet architecture, using the lease model, that is, rent and use, pay annually, so that the overall cost is very low, enterprises can afford to achieve low cost, fast deployment, easy operation and maintenance, which is also the charm of the Industrial Internet Where “.
3 The only way
However, one problem that needs to be pointed out is that although China’s high-tech and strategic emerging industries have developed rapidly in recent years, their industrial scale is not enough, and labor-intensive manufacturing is still the main body of China’s industrial development. Because they are export-oriented, such companies are basically at the low and mid-end of the global value chain, and their profit margins are not high. Therefore, the technological transformation is thin and the risks are high, making it difficult to promote the Industrial Internet.
Coupled with the lack of independent innovation capabilities of China’s key systems, software and hardware core technologies, industrial big data, industrial cloud and other key industrial Internet technologies, platforms and applications are still in their infancy, small scale and weak functions, which has led many companies to develop automation and industrial The Internet has doubts and is still on the sidelines.
Although the Industrial Internet is considered the foundation of the new industrial revolution, implementation requires a practical foundation.
From the evolution process of global manufacturing technology, lean production from semi-automated Taylor-Ford system to Toyota of Japan is an inevitable path. This is exactly the path that Chinese SMEs need to take to gradually increase the proportion of automated production and strengthen lean management.
Some front-line managers of enterprises told the author that the implementation of the Industrial Internet should be based on the accumulation of lean production.
However, judging from the status quo of enterprises in different industries, many of them still lack in carrying out lean production. In this case, even if the Industrial Internet is used, the results will be greatly reduced. Therefore, for these companies, if they want to develop the Industrial Internet, they must also make up the lessons of Industry 2.0 and Industry 3.0.
Looking back at the history of manufacturing transformation in developed countries in the world, it can be found that Japanese companies attach importance to organizational culture and human training. Production experience and knowledge depend on the accumulation, use, and inheritance of people. Therefore, the automation and information construction of enterprises mainly revolves around helping People go to work. But in recent years, this idea has been challenged by the growing problem of aging.
German companies pay attention to the continuous upgrading of equipment and production systems, solidify production knowledge on equipment, and the main strategy to cope with labor shortages is to develop more advanced equipment and highly integrated automatic production lines.
As the world’s high-end manufacturing powerhouse, the United States pays the most attention to the role of data in the way it solves problems. Not only does it attach importance to data accumulation, but more importantly, it also attaches importance to data analysis. Factual management culture.
In addition, immigration has become an important means to solve the problem of labor shortage and knowledge accumulation in the manufacturing industry. The high-end manufacturing industry in the United States is good at subverting and redefining problems, such as using the industrial Internet to subvert the value system of manufacturing, and using digitalization, new materials, and new production methods. (3D printing) to overturn production methods in traditional manufacturing.
If China’s manufacturing industry wants to occupy a favorable position in the new global technology and industrial competition, automation and informatization in the production and management process are the only way.
Although facing multiple challenges, due to the establishment of a relatively complete manufacturing system in China and the continuous consolidation of the network information technology foundation, the integration and development of manufacturing and the Internet have continued to deepen, laying a good foundation for the further development of the Industrial Internet.
The Industrial Internet essentially still depends on the upgrading and transformation of industrial technology of enterprises, and the advancement of information technologies such as 5G mobile communications, the Internet of Things, high-performance computing, and cloud computing can play a good role in assisting improvement.
Finally, another bottleneck in the future development of the Industrial Internet is the lack of talent.
In addition to advanced algorithm tools for industrial big data analysis, it is more important to combine domain knowledge of industrial scenarios and application principles. In other words, the analyst of the data must not only know the intelligent algorithm very well, but also the production system.
At present, enterprises are short of compound talents who understand both industrial production and information technology. The cultivation of such industrial big data analysis talents is difficult to cultivate in a short period of time. This requires special attention. It depends on the country and enterprises. And scientific research institutes and other parties work together to solve the problem.