Factory Audits are performed according to the standard of ISO9000 or customized requirements.It helps the clients to know if the factory has the ability to complete their order as required.
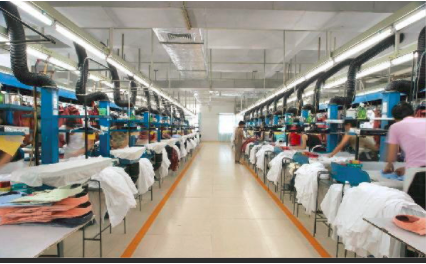
For a standard Factory Audit, it mainly covers the below fields:
Factory Profile
It is the general information about the factory, such as the factory’s foundation date, the work floor area, the main customers, the number of employees, the organization and the product main process etc.
Factory Facilities and Machinery Conditions
It gives some basic information about the machines and facilities, such as the number of machines, the machine type, the maintenance condition and the housekeeping situation etc.
Electric Power Supply and Delivery / Loading Condition
To check if the public power supply is stable, if the factory has enough back-up power generators when needed and the time from the factory to the airport or port etc.
Production Capacity
To check if the factory’s production capacity in terms of number of machines, workers and warehouse etc. can meet the order volume.
Quality Assurance system
To check the factory’s quality control process in procurement, equipment calibration, in-coming material, manufacturing, final products and customer’s complaint handling areas.
Hygiene and Security
To check if the employees are in a good and safe working condition.