1. Responsible for the post to carefully check and confirm the standards for all kinds of plastics, record the inspection results and quantity on the QC inspection report, calculate the number of qualified, number of rejected and defective rate of the day.
2. Responsible for notifying relevant management personnel of the detected defective products to take countermeasures immediately, and QC tracking and confirming the improvement effect.
3, Every time the product transfer, be sure to refer to the sample to confirm the appearance of oil injection/silk screen color, structure (insert) fitting is qualified.
4, Check the plastic products, must be light to handle light, bad products into the pull bottom, pay attention not to touch.
5. When the defective screen printing is detected, it shall be neatly placed on the defective product frame, and the name, reason, quantity, date and person in charge shall inform the shift leader to solve the problem immediately, and QC shall confirm the improvement effect.
6, when the injection QC inspection to beer plastic bad, immediately inform the group leader feedback injection QA review, when printing QC inspection to the injection non-conforming, immediately inform the injection QC review, when QA sampling to bad product, immediately inform the silk-screen QC review, when customer return bad product, QC inspection record against bad project, and analyzing the defective product causes, countermeasures and inform the related department and track the improvement effect.
7. During the shift handover, the QC shall explain the daily complaints on the production line, quality problems on the shift, handling methods, mold modification, newly issued technical documents and sample information, and make clear the handover, and both parties shall sign.
8. Always adhere to the concept of “7S” : ensure the cleanliness of the environment and the arrangement of materials within the work scope.
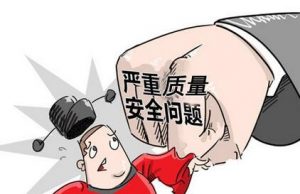
Matters needing attention for QC :
1. Do a good job in the statistics of basic data;
2. Analyze the direction and focus of improvement;
3. Further collect data for the target to be improved, and analyze the specific reasons for the improvement process;
4. Make specific plans for quality improvement;
5. Improve step by step.
6. Conclusion.